Machine time recording
Measure and monitor equipment times in real time, identify problems and reduce malfunctions
Analyse the times poured for each machine
Collect, analyse and manage your production data
Production time detection is one of the most important phases in the production plant.
The materialSUITE™ algorithmic rules have the purpose of calculating the OEE (Overall Equipment Effectiveness) of the plant and the interferences that cause production problems by limiting inactivity related losses.
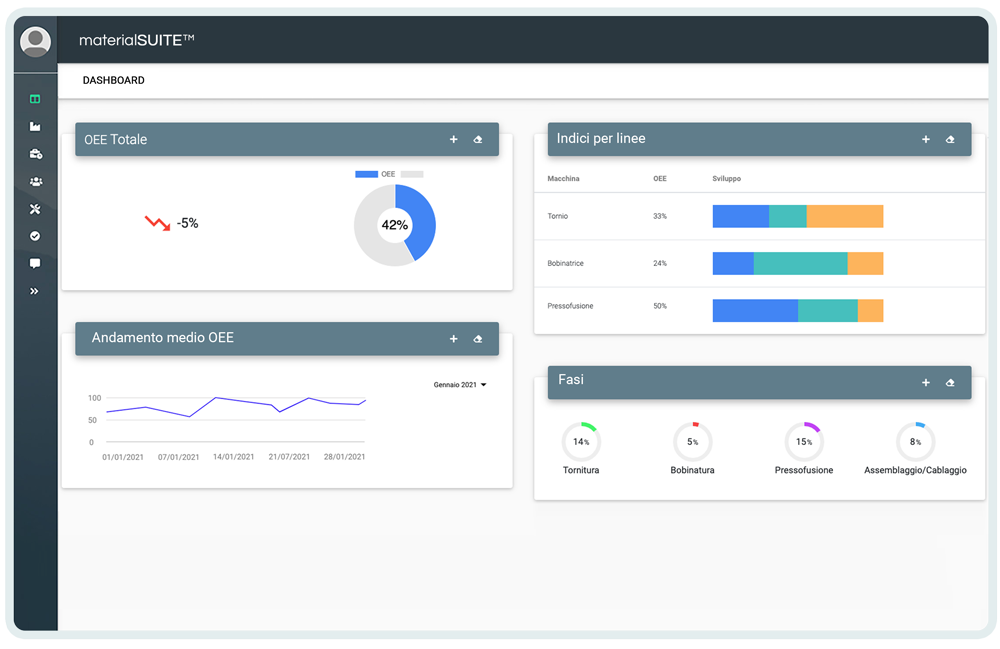
-
Streamlines production time inherent in equipment
-
Identify and manage production machinery malfunctions
-
Productivity loss identification
-
Progressive abandonment of paper
Connection between software and machinery to optimise remote control access
Through HMI, PLC or SCADA data collection systems, through standard protocols integrated into the suite such as OPC-UA, the MES module is able to show the operator the KOIs of the pant and of each individual machine: this allows to focus attention on specific phases, providing statistics like availability, quality and reliability thanks to machine status analysis.
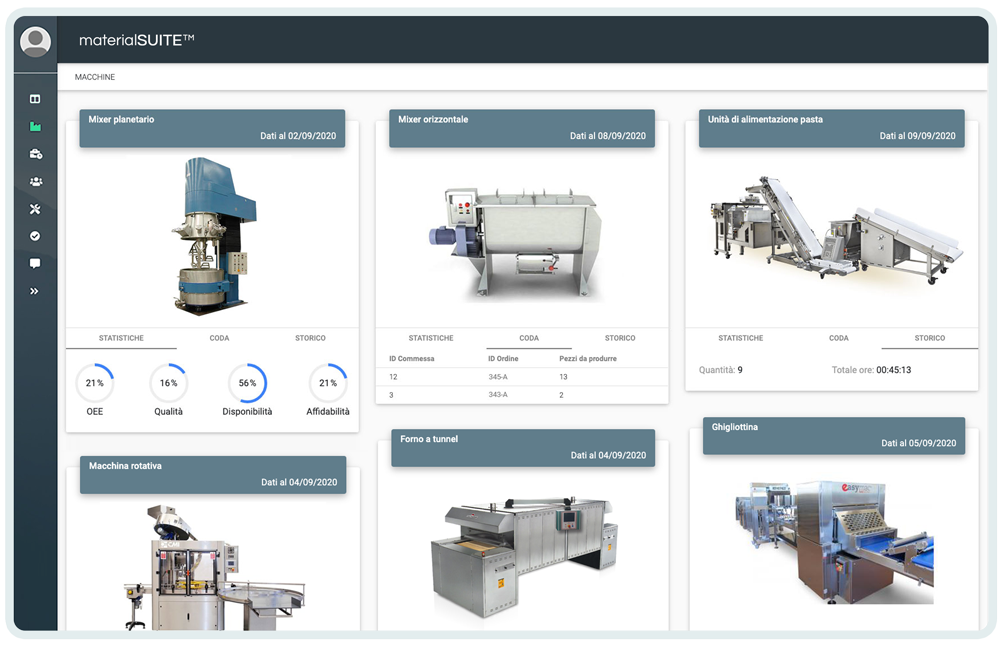
-
Cost and waste reduction to streamline production
-
4.0 connection and digitalisation of machinery
-
Consumption and resource use measurement during the production process
-
Machine condition checks in compliance with the process parameters
What are the advantages for the decision maker?
The function of recording production times and machine times involves a great profit in terms of production optimization because, thanks to the data acquired and the ease of reading of the same, Predictive maintenance can be established to prevent machine downtime and sudden plant shutdowns.
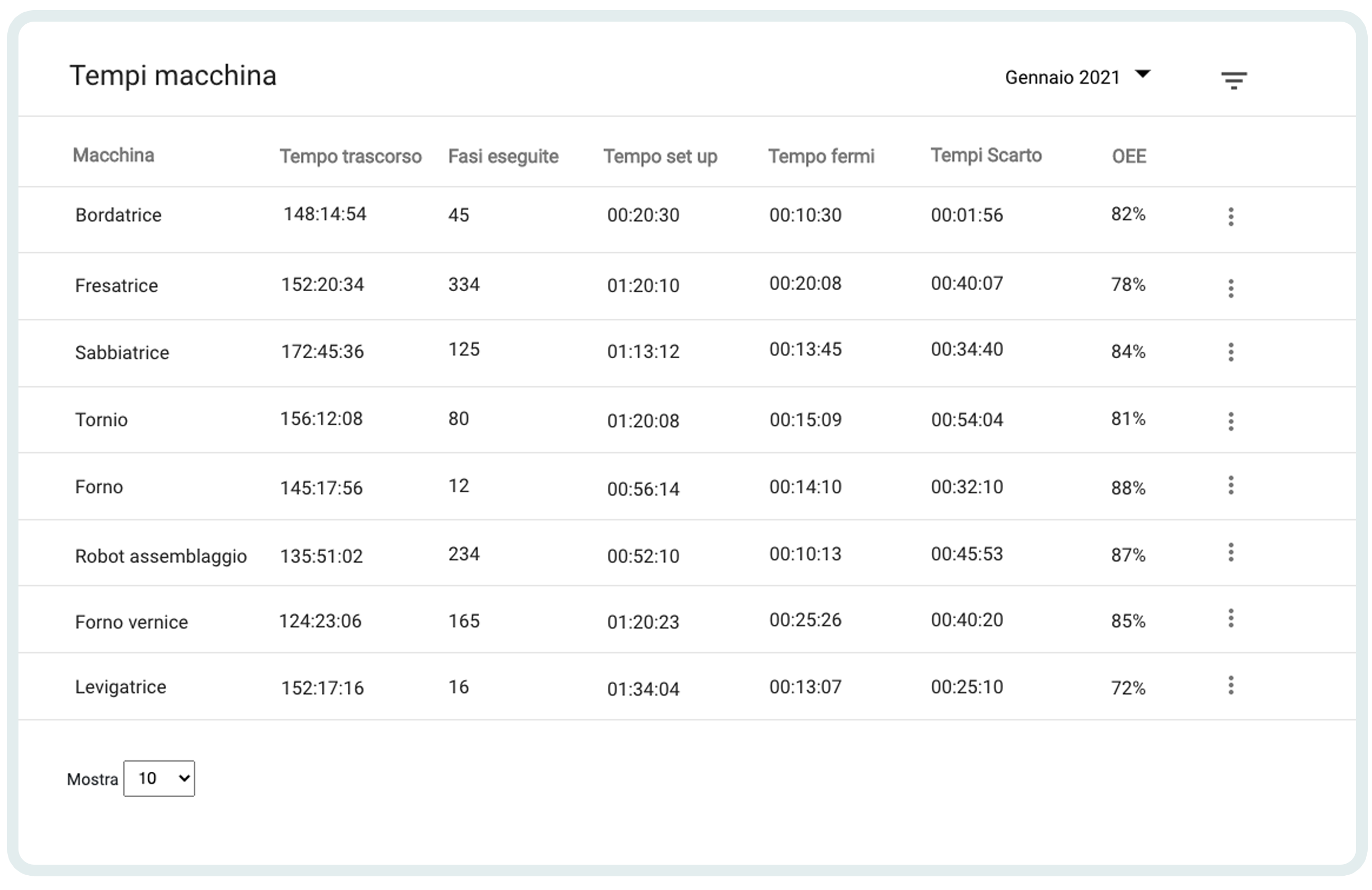
-
Identification and management of actual processing times
-
Equipment daily health check
-
Collect data on your production efficiency
-
Production process optimisation
The opportunities to be 4.0 industry
In order to measure production times and to benefit from industry 4.0 incentives, it is necessary that the machines are interconnected and that they have all the requirements required to be considered smart factory. The machines can provide a two-way communication, they can be configured remotely and it will also be possible to know their status in real time. The latter is a decisive factor in taking into account the advantages deriving from the automation of industrial production processes.